What is Porosity in Welding: Best Practices for Staying Clear Of Porous Welds
What is Porosity in Welding: Best Practices for Staying Clear Of Porous Welds
Blog Article
Porosity in Welding: Identifying Common Issues and Implementing Finest Practices for Avoidance
Porosity in welding is a pervasive concern that frequently goes undetected until it triggers significant problems with the integrity of welds. In this conversation, we will discover the key variables contributing to porosity development, examine its damaging impacts on weld performance, and go over the ideal methods that can be adopted to reduce porosity occurrence in welding procedures.
Typical Root Causes Of Porosity
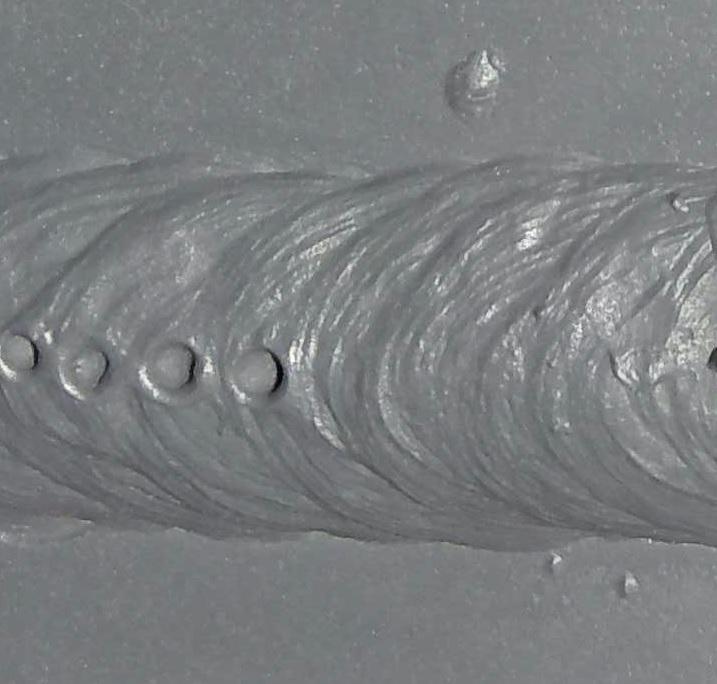
An additional frequent wrongdoer behind porosity is the visibility of impurities externally of the base steel, such as oil, grease, or rust. When these contaminants are not effectively gotten rid of prior to welding, they can evaporate and become entraped in the weld, creating flaws. Making use of filthy or damp filler products can introduce contaminations into the weld, contributing to porosity concerns. To reduce these usual reasons for porosity, thorough cleansing of base steels, appropriate protecting gas option, and adherence to ideal welding criteria are necessary techniques in attaining premium, porosity-free welds.
Effect of Porosity on Weld Quality

The presence of porosity in welding can dramatically jeopardize the structural honesty and mechanical properties of welded joints. Porosity produces gaps within the weld steel, compromising its total toughness and load-bearing capability. These spaces function as stress focus factors, making the weld extra prone to splitting and failing under applied loads. Additionally, porosity can decrease the weld's resistance to rust and various other ecological elements, additionally lessening its longevity and performance.
Welds with high porosity degrees often tend to exhibit lower impact stamina and lowered ability to warp plastically before fracturing. Porosity can hinder the weld's capability to successfully send pressures, leading to early weld failing and potential safety risks in crucial frameworks.
Ideal Practices for Porosity Avoidance
To enhance the structural stability and top quality of welded joints, what certain procedures can be applied to minimize the occurrence of porosity during the welding procedure? Porosity avoidance in welding is crucial to guarantee the integrity and toughness of the final weld. One reliable technique appertains cleansing of the base metal, eliminating any kind of contaminants such as rust, oil, paint, or moisture that can lead to gas entrapment. Making certain that the welding equipment is in great problem, with tidy consumables and proper gas circulation prices, can also dramatically minimize porosity. In addition, keeping a secure arc and managing the welding parameters, such as voltage, current, and take a trip rate, assists develop a consistent weld pool that reduces the threat of gas entrapment. Making use of the appropriate welding strategy for the certain material being bonded, such as readjusting the welding angle and weapon setting, can additionally avoid porosity. Routine assessment of welds and immediate removal of any type of issues identified during the welding procedure are vital practices to avoid porosity and produce top quality welds.
Value of Proper Welding Techniques
Carrying out appropriate welding methods is vital in guaranteeing the architectural honesty and top quality of bonded joints, constructing upon the foundation of efficient porosity read prevention procedures. Welding strategies directly impact the total toughness and toughness of the welded structure. One crucial element of correct welding methods is preserving the appropriate warm input. Too much warm can lead to boosted porosity due to the entrapment of gases in the weld swimming pool. On the other hand, insufficient warm might lead to incomplete blend, producing potential powerlessness in the joint. Furthermore, making use of the ideal welding specifications, such as voltage, existing, and take a trip rate, is vital for attaining audio welds with minimal porosity.
In addition, the choice of welding process, whether it be MIG, TIG, or stick welding, need to straighten with the particular demands of the task to make certain index optimal outcomes. Appropriate cleansing and preparation of the base metal, along with picking the read more appropriate filler material, are likewise necessary parts of skilled welding methods. By sticking to these best techniques, welders can decrease the danger of porosity development and produce top notch, structurally sound welds.

Testing and Quality Assurance Procedures
Quality control procedures play an essential role in confirming the stability and integrity of welded joints. Evaluating treatments are necessary to identify and protect against porosity in welding, making certain the strength and resilience of the end product. Non-destructive screening techniques such as ultrasonic testing, radiographic screening, and visual evaluation are frequently employed to determine potential defects like porosity. These techniques permit the evaluation of weld quality without compromising the integrity of the joint. What is Porosity.
Post-weld assessments, on the various other hand, assess the final weld for any type of issues, consisting of porosity, and validate that it meets defined requirements. Carrying out a comprehensive top quality control strategy that consists of detailed testing procedures and inspections is critical to minimizing porosity issues and ensuring the total top quality of bonded joints.
Final Thought
Finally, porosity in welding can be a typical concern that impacts the high quality of welds. By identifying the usual sources of porosity and carrying out ideal practices for prevention, such as proper welding methods and screening procedures, welders can make sure top quality and dependable welds. It is necessary to focus on avoidance techniques to minimize the occurrence of porosity and maintain the integrity of bonded frameworks.
Report this page